CSR
An outline of
DYNAX's
CSR activities
Environmental Conservation
In order to preserve the global environment, we have actively been striving to save energy, reduce CO2 emissions, reduce wastes and reuse resources.
Introduction of solar power generation
Tomakomai Plant introduces solar power generation and is working on utilization of renewable energy.
At the haed office, we have installed a carport with the solar panel, which can be used not only for our company-owned EV but also by visitors'.
We have installed a solar power generation facility in our on-site childcare facility and have realized a virtually zero CO2 emissions facility.
We have introduced carport-type solar power generation systems at Chitose and Tomakomai plants, and are working to utilize renewable energy.
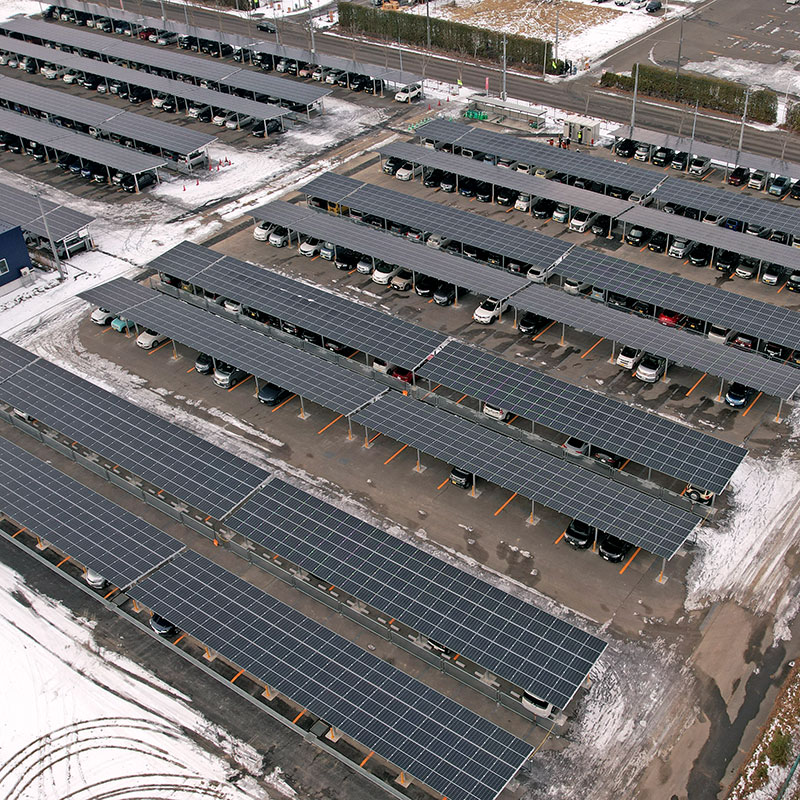
Chitose Plant
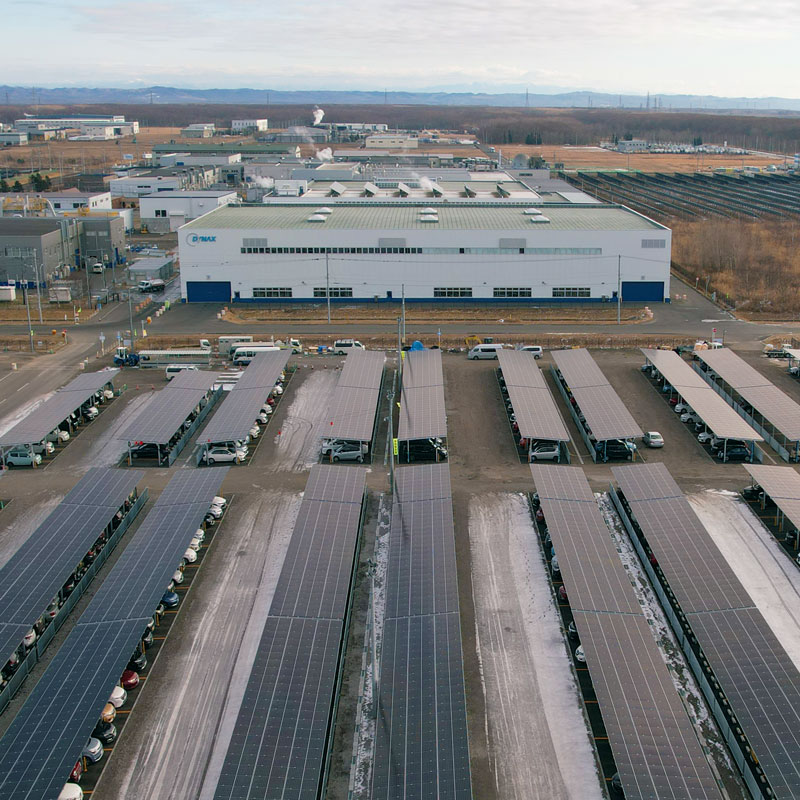
Tomakomai Plant
We have introduced solar power generation at Chitose plant and are working to utilize renewable energy.
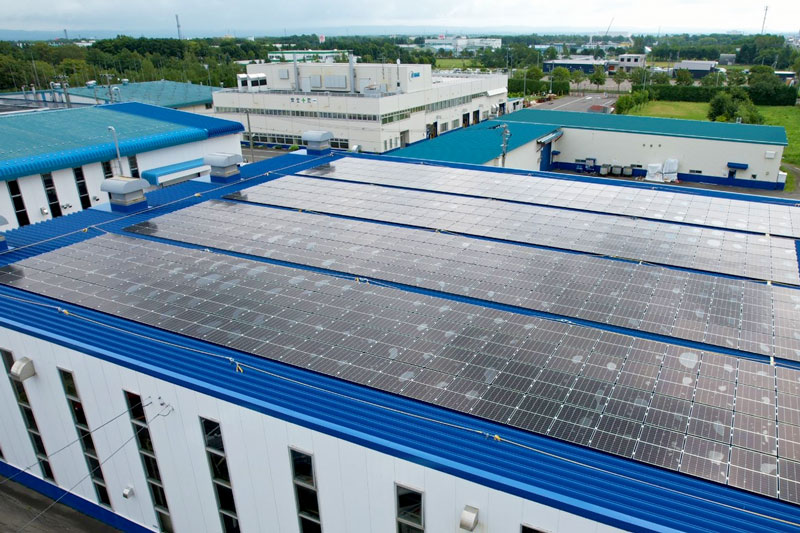
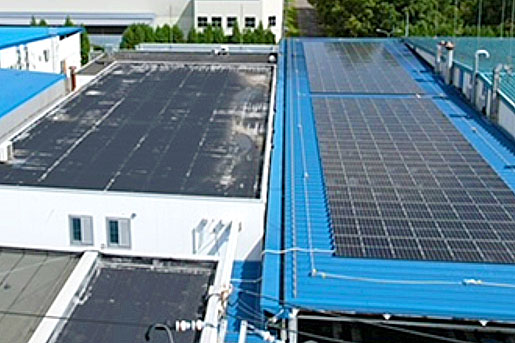
We have introduced a biomass boiler that uses wood chips to reduce gas consumption.
Replacement with LED lighting
We are proactively pursuing to replace current lighting system with low-power-consumption and low-CO2-emission LED lighting for both factory and office.
Utilization of exhaust heat from production processes
Introducing an exhaust gas boiler, we reuse waste heat generated during impregnation processes for heating and production lines to reduce gas consumption
※ An impregnation process is the process of immersing friction material base paper in resin and baking it.
Improvement of friction material yield
The friction material used in a clutch disk, one of our main products, used
to mainly be punched out in a ring shape from raw sheets, but now it is
increasingly punched out into small pieces (dots) and assembled on to a
disk per its specification.
By adopting this method, material yield has been dramatically improved,
contributing to the reduction of waste. In addition, with these products, we
can respond to customers' various detailed demands for performance
and characteristics, and, in turn, are also helping to improve the fuel
economy of our customers' vehicles.
For conventional ring shape, material yield is improved by punching multi
rings with different diameters at the same time in nesting.
-
Environment Policy
Environmental Vision
Basic Policy -
Environmental Management
Management System
Management Committee
Internal web site
Certification of ISO14001 -
Environmental Conservation
Gas cogeneration system
Solar power generation
Replacement with LED lighting
Utilization of exhaust heat -
Contribution to Environment by Product Development
Product Development
for Low CO2 Emission
Our environmental technology
and development history -
Environmental Performance Data
Water Quality
PRTR Target Substance -
Coexistence with society
Cleaning activities
around the plant
Dynax Children's Club Flowerbed